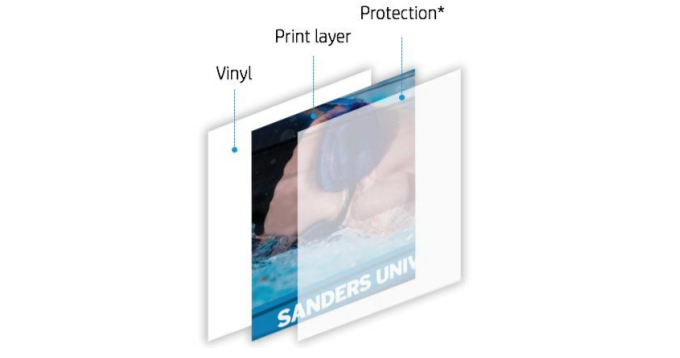
Printed surfaces should be protected according to the customer’s requirements.
Warranting a Graphic
The liquid laminate developed by 3MTM for HP Latex is called Screen Print UV Gloss Clear 9760LX, and it includes a 3MTM MCSTM warranty of up to 5 years for laminated graphics. As a fleet graphics service provider you will also provide a warranty, therefore you will want to specify how the graphic should be produced and installed.
For cars, vans, and trucks, a 5-year warranty is normally given in most cases, while for public transportation, one is usually not needed (due to the frequent change of vehicle graphics).
As the material manufacturer, your warranty will cover the complete finished graphic:
- Material
- Ink
- Protection
The table below gives you an idea of how long you should warrant your laminated graphics.
For more information about the 3MTM MCSTM warranty, visit http:// www.3m.com.
3MTM Screen Print UV Gloss Clear 9760LX description
Product application considerations
Over-laminate can be a film or a liquid clear coat. Clear coats can be applied with a roll with a roll-to-roll laminator, or to sheets after cutting using a screen print process.
As for the characteristics of the 9760LX clear coat, it is a very glossy and thin coating. Compared to glossy paper, it creates a surface that is twice as glossy. The recommended thickness to apply is between 6 and 12 microns. The clear coat is designed to be applied by screen printing and to then be UV cured.
As for the workflow, you will trim the sheet, then put it under the screen printing device, which will apply the product. Then you will lift the screen and move the sheet to the laminator.
End-to-end HP, 3MTM, and FotobaTM solution to produce truck panels
Please see the section below to address the major parameters that should be controlled during the lamination process in order to ensure correct application and prevent issues such as cracking and stickiness.
For the full specifications on the application requirements as well as considerations in regards to the warranty, please refer to the 3MTM Product Bulletin 9760LX on 3M's website.
Here is a brief outline covering certain appliance considerations. As described above, there are 5 main steps to the lamination process:
- Apply the coat over the printed and trimmed panel.
- Cure the coated material in a UV oven.
- Contour cut if necessary.
- Apply masking tape when necessary in case of non-panel production.
- Apply the protected art on the truck, car or van.
There are 3 parameters that strongly need to be considered as per 3M’s recommendations:
- Web thread density:140-150 threads/inch at 31-34 microns threads. Incorrect web thread density will lead to:
- Incorrect distribution of the clear coat over the surface, causing issues with gloss uniformity, if not distributed well enough, or
- Cracking due to an excess of the product.
- Curing power and time: Curing lamp power needs to be 600 nw/cm2 and curing speed has to match; and exposure: 200 w/inch. If both parameters are incorrectly settled, it will lead to a lack of curing. Incorrect curing will be manifested as yellowish issues and stickiness over the surface.
- Masking tape must be under its own, separate 3MTM Masking Tape Bulletin guidelines.
Finally, please follow the recommendations in the Product Bulletin prior to applying the laminate.